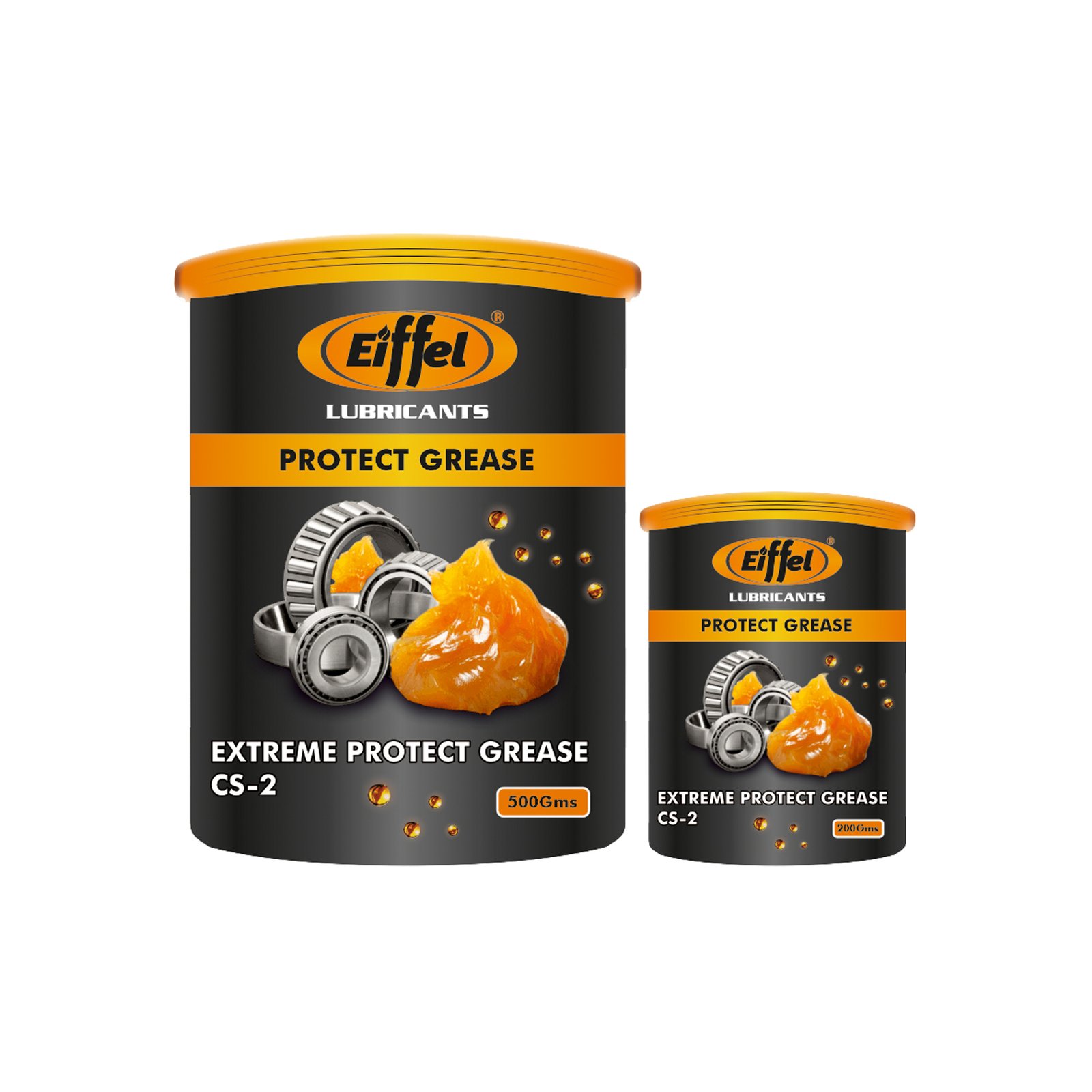
Calcium Sulphonate complex soap developed by Eiffel Lubricants allows Eiffel Xtreme Protect Grease CS-2 to work well in bearings even if rotation speeds are high. Presents outstanding performances even at high nDm where the NEW GENERATION keeps all benefits in terms of corrosion protection, bearings lifetime, high loads and thermal resistance.
Excellent anti-oxidation and anti-corrosion properties thanks to the excellent behavior of the calcium sulphonates, also in the presence of sea water.
The NEW GENERATION of calcium sulphonate complex soap allows to keep outstanding performances even in case of high speed applications where normally polyurea or lithium complex greases are requested.
Does not contain lead, or other heavy metals considered harmful to human health and the environment.
Suitable for the lubrication of continuous castings and rolling mills in steel plants, bearings in wet and dry (felt rolls) sections of paper mills and all industrial applications under severe conditions (wet, loaded, high temperature, dust, etc.,)
Suitable for the lubrication of all kinds of components subject to high loads, shock loads, working in conditions where the grease is in frequent contact with water (even in sea water due to enhanced antirust performance of the grease).
Suitable for use in centralized greasing systems.
Always avoid contamination of the grease by dust and/or dirt when applying.
Preferably use a pneumatic pump system.
Specifications
Meets & exceeds the following Industry specifications
Typical Characteristics
Eiffel Xtreme Protect Grease | Test Method | Units | CS-2 |
---|---|---|---|
NLGI Grade | ASTM D 217/DIN 51 818 | – | 1-2 |
Thickener Type | — | — | Calcium Sulphonate |
Penetration, Worked @ 25 0C | ASTM D 217/DIN 51 818 | 0.1mm | 280-310 |
Penetration, Worked @ 25 0C, after 100,000 strokes | ISO 2137 | 0.1mm | +11 |
Shell Roller 100 hours at 80°C | ASTM D 1831 mod | 0.1mm | -8 |
Shell Roller 100 hours at 80°C + 10% water | ASTM D 1831 mod | 0.1mm | -12 |
Kinematic viscosity of the base oil at 40°C | ASTM D 445/DIN 51 562-1/ISO 3104/ IP71 | mm²/s (cSt) | 220 |
Operating temperature range | °C | -30 to 180 | |
Antirust properties | |||
EMCOR, distilled water | ISO 11007 | Rating | 0-0 |
EMCOR, synthetic sea water | ISO 11007 | Rating | 0-0 |
Copper corrosion, 24 hours at 100°C | ASTM D 4048 | Rating | 1b |
Antiwear and EP properties | |||
Four ball wear (scar diameter) | ASTM D 2266 | mm | 0.37 |
Four ball weld load | ASTM D 2266 | Kgf | 500 |
Cold properties | |||
Penetration at -20°C | ISO 13737 | 0.1mm | 160 |
Flow pressure at -20°C | DIN 51 805 | >mbar | >560 |
Flow pressure at 1400 mbar | DIN 51 805 | °C | -30 |
Torque at -20°C Starting torque After 1 hour | ASTM D 1478 | g.cm g.cm |
2600 460 |
Thermal Stability | |||
Dropping point | IP 396/ASTM D566 | °C | >300 |
Oxidation stability at 99°C +0.5°C Pressure drop after 100 hours Pressure drop after 500 hours |
ASTM D 942 | Psi Psi |
4 13.5 |
Oil release 50 hours, 100 °C | ASTM D 6184 | % | 1.4 |
Oil release 168 hours, 40°C | NF T 60-191 | % | 0.9 |
The above figures are typical of blends with normal production tolerance and do not constitute a specification.